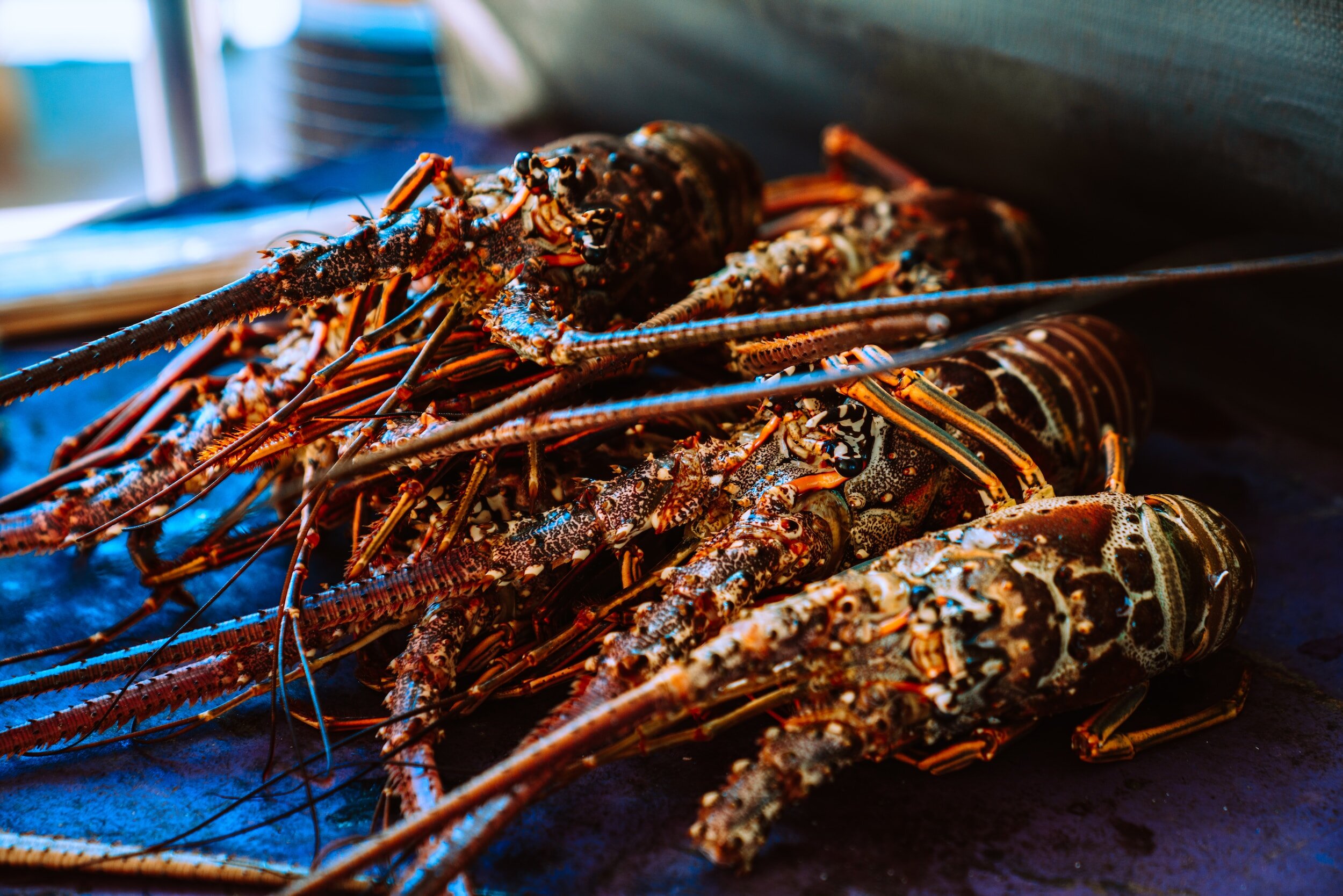
SEAFOOD
CMP was founded in 1956 with a primary focus on delivering processing equipment solutions to the seafood industry. While we have grown our company to now serve multiple food process markets worldwide, we have never forgotten our roots firmly set in the seafood industry.
With a focus on the shellfish industry, CMP specializes in providing turn-key seafood process lines. We take full responsibility for the installation and commission of our equipment. We also offer training for the operations personnel to ensure our customers maximum value and return on their investment.
Whether it is crab, lobster, mussels, salmon, clams, oysters, scallops, ground fish, pelagic, or shrimp – we have a process solution to meet your needs.
CASE STUDY
CASE STUDY
End-to-End Solutions:
Canadian Lobster Processing Plant - Complete Line
Challenge
1/ Atlantic Canada fresh lobster processor. Greenfield plant with multiple lobster products.
2/ Raw frozen lobster tails, cooked in shell and cooked lobster meat. Customer required plant layout and all equipment required.
Solution
Complete Line: custom design and build for processing raw and RTE lobster products, including a butchering line, sanitary conveyors, steam cooker, cooler, picking table, vacuum sealer, and shell waste management.
Result
1/ State-of-the-art processing lines utilizing ergonomic working stations, atmospheric steam for cooking multiple products simultaneously, and full RTE room equipment.
2/ 4,000lb per hour production rate achieved. Capable of steam cooking, cooling, meat picking and brine freezing, and packaging.
CASE STUDY
End-to-End Solutions:
USA Lobster Processing Plant - Complete Line
Challenge
1/ US based fresh lobster processor. Greenfield plant with multiple lobster products.
2/ Raw frozen lobster tails, cooked in shell and cooked lobster meat. The client required a layout and a full list of equipment.
Solution
Complete Line: custom design and build for processing raw and RTE lobster products, including a butchering line, sanitary conveyors, steam cooker, cooler, picking table, and shell waste management.
Result
1/ State-of-the-art processing lines utilizing ergonomic working stations, convection steam for cooking multiple products simultaneously, and full RTE room equipment.
2/ Targeted throughput rates met and quality of finished product exceeded customers' expectations.
CASE STUDY
End-to-End Solutions:
Mussel Processing
Line
Challenge
Atlantic Canada fresh mussel processor with aging equipment that was inefficient, damaging products, and could not meet the demand of their customers. Looking for a system that uses modern technology and sanitary design (easy to clean).
Solution
1/ Full mussel line including declumper, wet hopper, debysser, shaker, hygienic conveyors, meat harvesting, and integrated controls.
2/ Line fully tested with product prior to shipping to the facility.
Result
1/ CMP design and build of a new complete cleaning line for fresh mussels.
2/ Targeted throughput rates met, and quality of finished product exceeded customers' expectations.